Oil tubes are an essential part of machinery, as they are responsible for transporting oil to various parts of the equipment to ensure smooth operation. Over time, oil tubes can deteriorate and need to be maintained or replaced to prevent malfunction and damage to machines. In this article, we will discuss the main considerations related to maintaining and replacing oil tubes in machines.
Regular inspection
Regular inspection of the oil tubes is crucial to identify any signs of wear. A visual inspection can be performed to check for kinks, cracks, corrosion or leaks in the tubes. Additionally, pressure tests can be carried out to ensure that the tubes are able to withstand the required pressure. Any signs of damage or weakness should be addressed immediately to avoid potential oil tube failure.
Oil quality monitoring
The quality of the oil circulating in the tubes can have an impact on their lifespan. Contaminants in the oil can cause corrosion and blockages in the tubes, leading to reduced efficiency and potential machine breakdown. It is important to monitor the quality of the oil and ensure that it meets the manufacturer’s specifications. Regular oil analysis can be performed to identify any contaminants and take appropriate steps to maintain oil cleanliness.
Correct installation
When replacing oil tubes, it is crucial to ensure they are installed correctly to avoid future problems. This involves using tubing of the appropriate size and material, securing it in place to prevent movement, and using appropriate fittings and connectors. Improper installation can lead to leaks, blockages and other problems that can affect the proper operation of the machines.
Choosing the right material
The material of the oil tubes is an important factor to consider when replacing them. Different materials have different properties, such as resistance to corrosion, temperature and pressure. It is important to choose a material compatible with the type of oil used and the conditions in which the machine operates. Stainless steel, copper and aluminum are commonly used materials for oil tubing, each with their own advantages and limitations.
Consider environmental factors
The environment in which machines operate can impact the life of oil tubes. Factors such as temperature, humidity and exposure to corrosive substances can affect the integrity of the tubes. It is important to consider these factors when maintaining and replacing oil tubes and taking appropriate measures to protect them from environmental hazards.
Follow manufacturer’s instructions
Finally, it is important to follow the manufacturer’s guidelines for maintaining and replacing machine oil tubes. This includes using recommended materials, following prescribed maintenance schedules, and following proper installation practices. Any deviation from the manufacturer’s guidelines can result in premature failure of oil tubes and potential damage to machinery.
In conclusion, servicing and replacing oil tubes in machines is an essential aspect of equipment maintenance. Regular inspection, monitoring oil quality, proper installation, choosing the right material, considering environmental factors and following manufacturer guidelines are key considerations when it comes to ensuring the longevity and efficiency of oil tubes in machines. By paying attention to these factors, operators can prevent potential breakdowns and keep their equipment running smoothly.
Key Considerations for Maintaining and Replacing Oil Tubes in Machinery
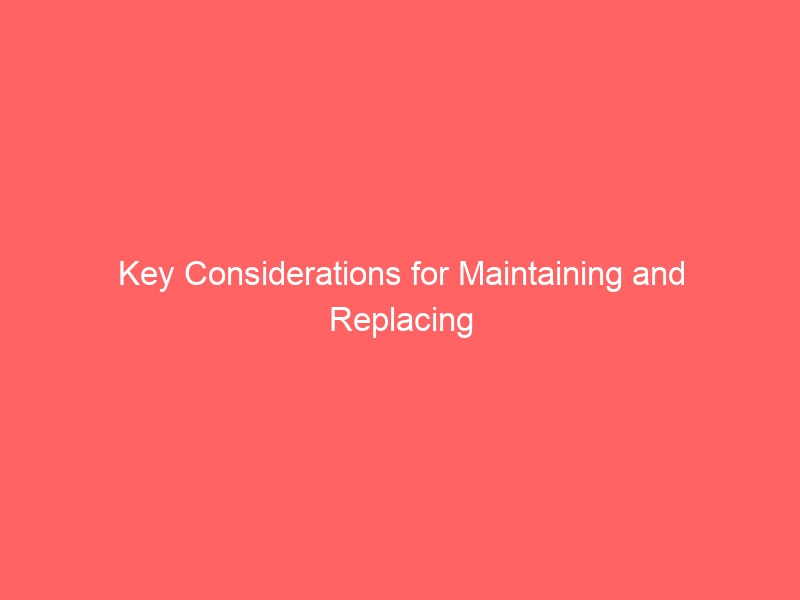