Unlocking the potential of the 1/2 burner with flexible fuel hoses: a game changer for industrial applications
The industrial sector has long relied on burners to provide the heat and energy needed for various manufacturing processes. However, traditional burner systems have limitations in flexibility and fuel adaptability. This is where innovative flexible fuel line technology comes into play, providing a revolutionary solution for industrial applications.
The 1/2 burner is an essential part of industrial processes, as it is responsible for converting fuel into thermal energy. However, the type of fuel used and the quality of combustion can have a considerable impact on the efficiency, performance and environmental impact of the burner. This is where flexible fuel hoses come in, providing a solution that allows burners to accommodate different types of fuels, including natural gas, propane, diesel and biofuels.
The concept of flexible fuel lines is based on the use of specially designed piping systems that can accommodate a wide range of fuels without compromising performance or safety. These pipes are equipped with advanced materials and engineering techniques that ensure they can handle the unique characteristics of different fuels, such as variations in pressure, temperature and chemical composition.
One of the main advantages of flexible fuel hoses is their ability to allow burners to switch between different fuels without requiring significant modifications or overhauls. This flexibility allows industrial facilities to adapt to changing fuel availability, cost fluctuations and environmental regulations, providing a significant advantage in operational flexibility and cost savings.
In addition to fuel flexibility, flexible fuel hoses also offer improvements in combustion efficiency and emissions control. The advanced technology used in the design of these pipes ensures that fuel is delivered to the burner in a precise and controlled manner, thereby optimizing combustion and reducing the formation of harmful pollutants such as nitrogen oxides and carbon monoxide.
Additionally, the use of flexible fuel lines can also contribute to the overall reliability and longevity of the system. By adapting to different fuels and maintaining efficient combustion, these pipes can reduce burner wear, improve operational stability and minimize the risk of downtime and maintenance issues.
The potential applications of flexible fuel lines are numerous, ranging from industrial boilers and furnaces to thermal oxidizers and power generation systems. These pipes can be integrated into new and existing burner systems, providing a cost-effective and sustainable solution for a wide range of industrial processes and applications.
In conclusion, the use of flexible fuel pipes presents a revolutionary opportunity for industrial applications, unlocking the potential of the 1/2 burner to adapt to different fuels, improve combustion efficiency and reduce emissions. As the industrial sector continues to evolve and face challenges related to fuel availability, environmental regulations and cost pressures, flexible fuel lines offer a valuable solution that can improve operational flexibility, sustainability and performance. Industrial facilities that adopt this innovative technology will gain a competitive advantage and contribute to a more sustainable future.
Unlocking the potential of the 1/2 burner with flexible fuel hoses: a game changer for industrial applications
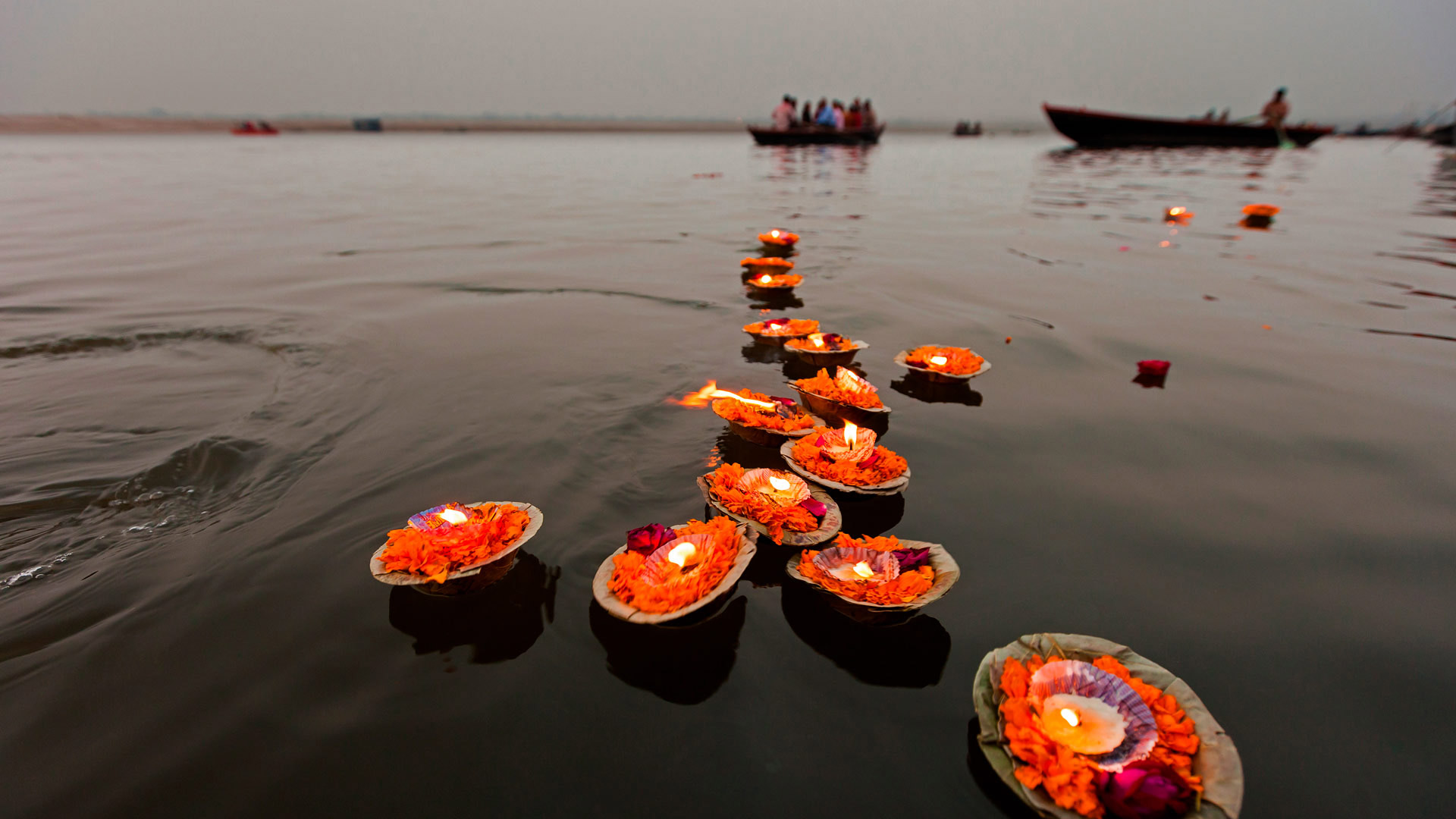