Flexible burner fuel pipes are a crucial part of industrial heating systems, enabling the efficient and reliable delivery of various fuels to the combustion process. These pipes are designed to withstand high temperatures, corrosive environments and the physical stresses of industrial operations. Understanding the technology behind flexible fuel hoses is essential to ensuring their proper functioning and longevity.
Flexible fuel pipes for burners are typically made from high quality materials such as stainless steel or high temperature alloy to withstand the harsh conditions of industrial combustion processes. These materials are selected for their corrosion resistance, resistance to high temperatures and mechanical strength. The design and construction of these pipes is essential to ensure that they can efficiently deliver a wide range of fuel types and withstand the demands of industrial applications.
The technology behind flexible fuel hoses involves a combination of advanced materials, manufacturing techniques and engineering expertise. These pipes are often constructed using techniques such as welding, seamless tubing and precision bending to ensure the highest level of performance and reliability. Advanced welding techniques, such as orbital welding, are often used to create airtight, leak-free connections that can withstand the high pressures and temperatures of industrial burners.
In addition to the materials and construction techniques used, the design of flexible fuel lines is essential to their proper operation. Pipes must be designed to accommodate the various fuels used in industrial applications, such as natural gas, propane, diesel or biofuels. This requires careful consideration of factors such as flow rates, pressure requirements and thermal expansion to ensure the pipes can deliver fuel to the burner safely and efficiently.
Flexible fuel hoses for burners also incorporate advanced technologies to improve their performance and longevity. For example, thermal insulation can be applied to pipes to reduce heat loss and maintain the temperature of the fuel as it travels to the burner. Corrosion-resistant coatings or coatings can also be applied to protect pipes from the corrosive effects of certain fuels and combustion byproducts.
Proper installation and maintenance are crucial to ensure the performance and longevity of flexible burner fuel pipes. These pipes must be installed and connected to precise specifications to ensure safe and efficient fuel delivery. Regular inspection and maintenance is also essential to identify and resolve any issues that may compromise pipeline performance and safety.
In conclusion, the technology behind flexible burner fuel pipes involves a combination of advanced materials, construction techniques and engineering expertise to ensure their proper operation and longevity in industrial combustion processes. Understanding this technology is essential to selecting, installing and maintaining these critical components to ensure safe and efficient industrial heating operations.
Understanding the Technology Behind the Flexible Fuel Hose for the 1/2 Burner – A Deep Dive
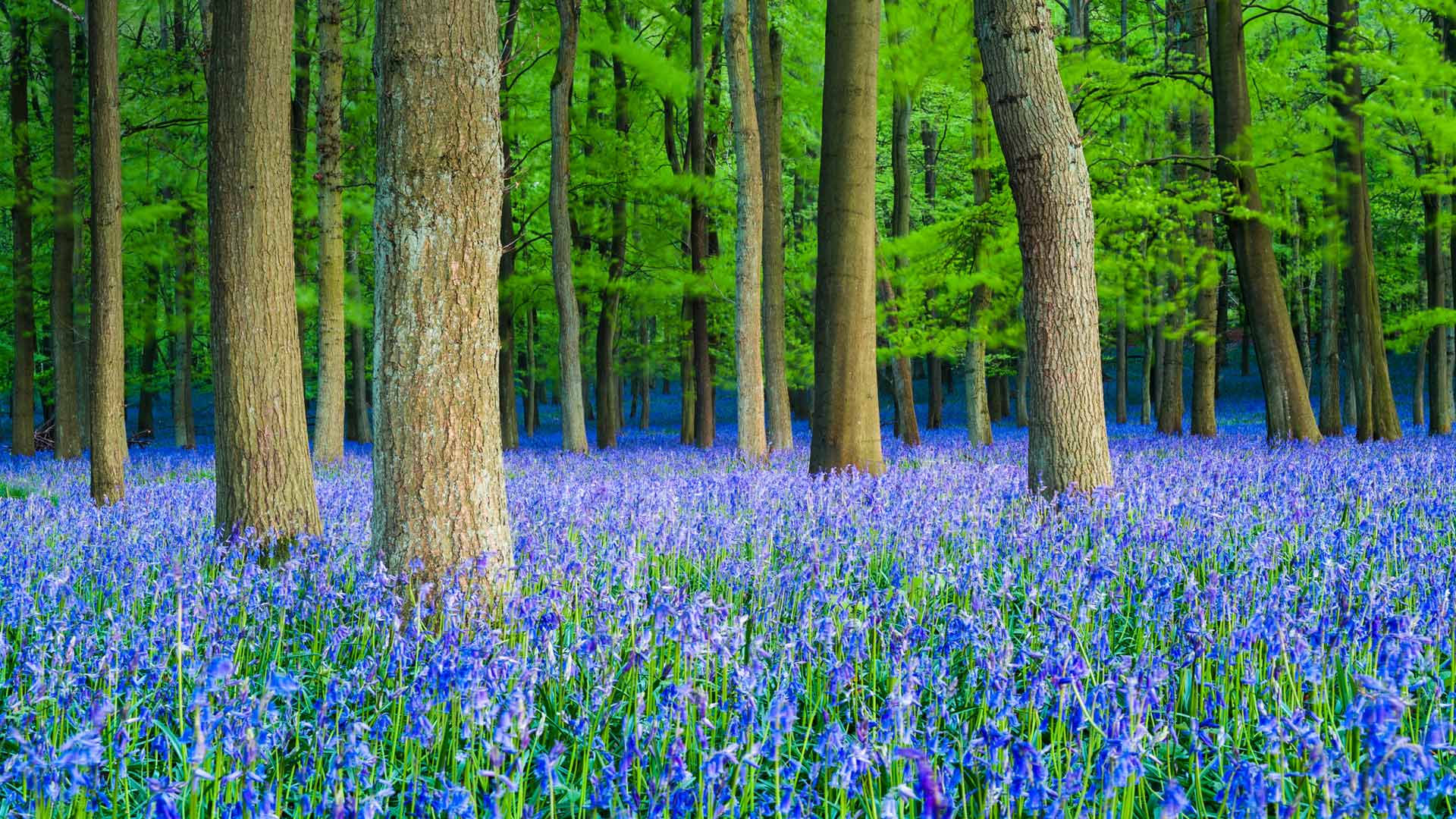