Combustion burners are a key part of industrial processes, playing a vital role in generating heat for a wide range of applications. From powering boilers, furnaces and drying ovens to providing heat for chemical reactions and material processing, combustion burners are integral to the effective and efficient operation of countless industrial processes .
One of the main functions of combustion burners in industrial processes is the generation of heat for various thermal applications. In industries such as oil and gas, petrochemicals, food processing and automobile manufacturing, controlled combustion of fuel in burners is essential for heating raw materials, producing steam and maintaining specific temperatures in processes of production. This heat is crucial for a wide variety of processes, including drying, curing, melting and sterilization.
In addition to providing heat, combustion burners are also used in industries such as metal smelting, glass manufacturing, and cement production to facilitate chemical reactions requiring high temperatures. The combustion process in these applications serves not only to generate heat but also to create an environment conducive to specific chemical transformations. In metal smelting, for example, combustion burners are used to melt metal ores, while in the glass manufacturing industry they enable the melting and shaping of glass materials.
In addition, combustion burners play an essential role in the production of electricity in thermal power plants. These power plants rely on burning fossil fuels, such as coal, natural gas and oil, to power turbines and generators, which then produce electricity. The efficient and controlled operation of combustion burners is essential to ensure the stability and reliability of electricity production in these installations.
The type of combustion burner used in industrial processes depends on the specific application requirements. For example, industrial burners can be classified based on the type of fuel they use, such as gas, oil or biomass, or based on their design and combustion method, such as atmospheric burners, burners regenerative or radiant tube burners. Each type of burner is selected based on factors such as the heat output required, the type of fuel available and the environmental regulations to be respected.
While combustion burners are essential to industrial processes, they also present challenges, particularly in terms of environmental impact and energy efficiency. Burning fossil fuels in industrial burners releases emissions such as carbon dioxide, nitrogen oxides and particulate matter, which can contribute to air pollution and climate change. As a result, there is an increasing focus on developing cleaner combustion technologies and improving the energy efficiency of combustion burners. This has led to the adoption of advanced combustion systems, such as low NOx burners, flue gas recirculation and air-fuel ratio control, which aim to minimize emissions and optimize utilization fuel.
In conclusion, combustion burners are an essential part of industrial processes, serving as the primary means of heat generation for a wide range of applications. They play an essential role in heating, chemical reactions, electricity generation and material processing in all industrial sectors. As industrial operations continue to evolve, there is an increasing focus on developing more efficient and environmentally friendly combustion technologies to meet the demands of the modern industrial landscape.
The role of combustion burners in industrial processes
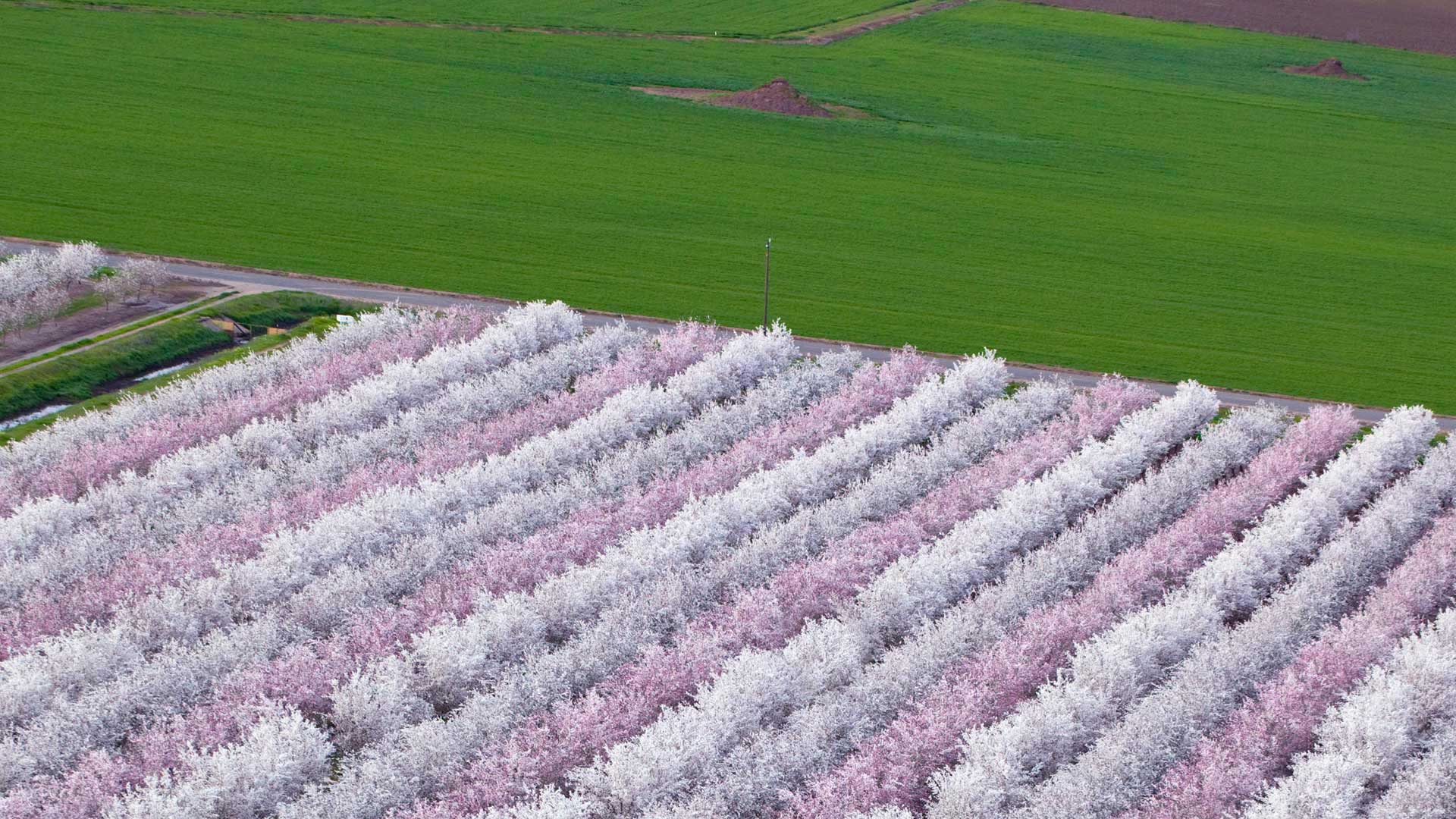