When it comes to burner systems, fuel flexibility is crucial to ensure optimal performance and efficiency. The ability to use different fuel types allows for greater versatility and adaptability, making it easier to meet changing energy demands and environmental regulations. In this guide, we will focus on the importance of fuel flexibility in burner systems, particularly in the context of 1/2” pipe.
1/2” pipes are commonly used in burner systems to transport fuel from the storage tank to the burner. These pipes are usually made of steel or stainless steel and are designed to withstand high temperatures and pressures. Pipe size plays a critical role in the flow rate and efficiency of the burner system, making it important to carefully consider fuel compatibility when selecting the appropriate pipe size.
Fuel flexibility in burner systems allows for the use of a wider range of fuels, including natural gas, propane, diesel and biofuels. This versatility is especially important in industries where fuel availability and cost can vary widely. By being able to switch between different fuel sources, burner systems can adapt to changing market conditions and minimize downtime and operating costs.
In addition to economic benefits, fuel flexibility also offers environmental benefits. By using alternative fuels such as biofuels or renewable sources, burner systems can reduce greenhouse gas emissions and promote sustainability. This is particularly important in sectors where reducing the carbon footprint is a priority and regulatory compliance is mandatory.
To ensure optimal performance and efficiency, it is important to consider the compatibility of different fuels with 1/2” pipes. Some fuels, like natural gas and propane, burn relatively cleanly and have a low viscosity, making them suitable for use with smaller sized pipes. Other fuels, such as diesel or biofuels, may have a higher viscosity or contain impurities that can cause smaller pipes to clog or corrode.
To maintain fuel flexibility in burner systems with 1/2” pipes, it is important to regularly inspect and clean the pipes to prevent buildup and blockages. Additionally, using high-quality materials and fittings, such as corrosion-resistant steel or stainless steel, can help extend the life of pipes and ensure safe and efficient operation.
Overall, fuel flexibility is a key factor in ensuring the reliability and efficiency of burner systems with 1/2” pipes. By choosing the right fuel sources and maintaining the appropriate infrastructure, industries can maximize their energy efficiency, reduce operational costs and minimize environmental impact. As technology continues to advance, the importance of fuel flexibility will only increase, making it a crucial element to consider in the design of any burner system.
The Importance of Fuel Flexibility in Burner Systems: A Guide to 1/2” Pipe
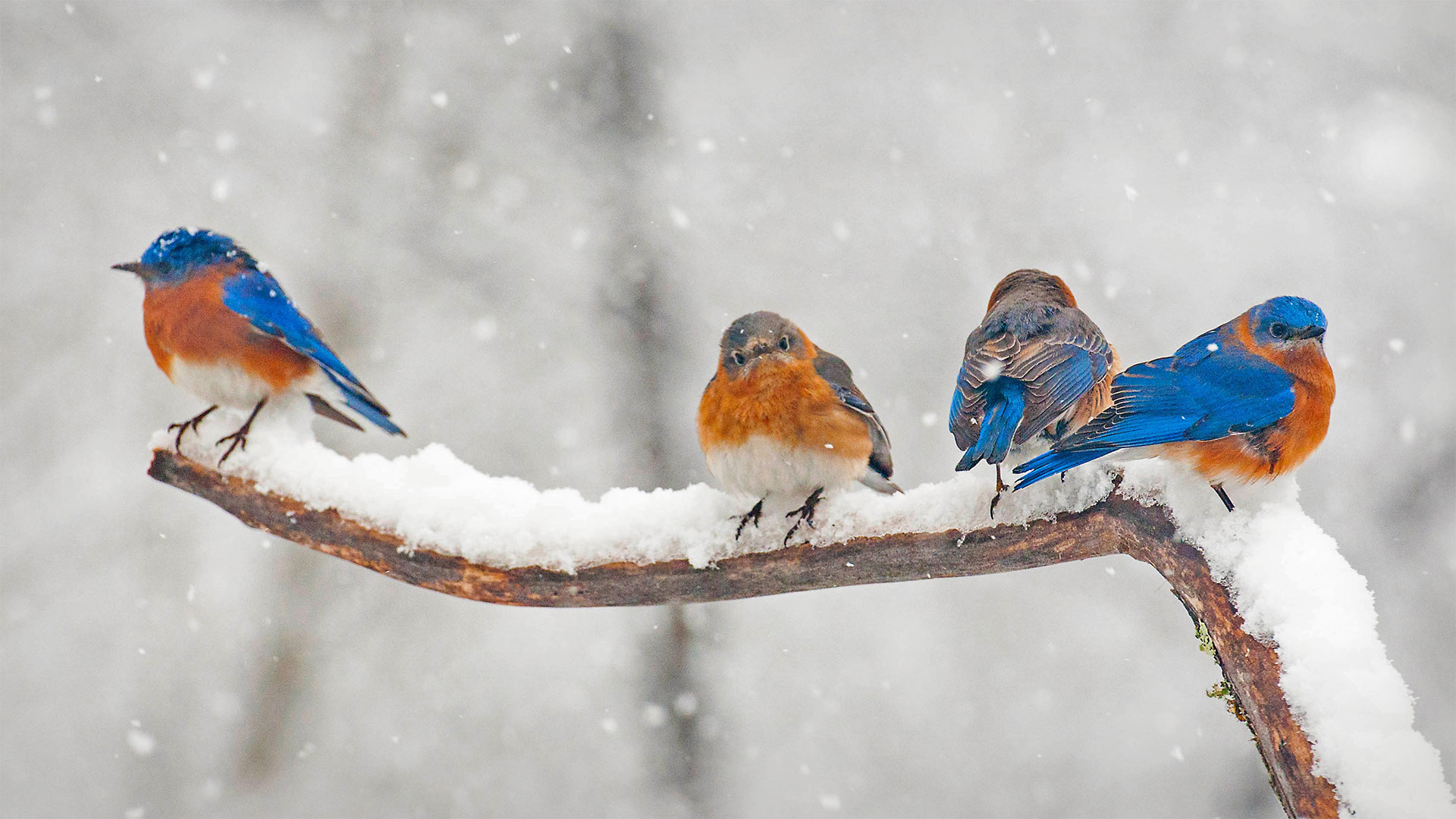