Burner pipes are an essential component in various industrial processes, such as power generation, refining and chemical production. They play a crucial role in burning fuels to generate heat for boilers, furnaces and other heating applications. However, the type and quality of fuel used in these processes can vary considerably, making fuel flexibility a critical factor in the design and operation of burner lines.
The importance of fuel flexibility in burner pipes cannot be overstated. With the growing focus on energy diversification and sustainability, industries are turning to a wider range of fuel sources, including natural gas, diesel, biofuels and even waste. This trend requires burner pipes to be able to handle different fuel compositions, viscosities and calorific values without sacrificing performance or efficiency.
One of the key benefits of fuel flexibility in burner lines is the ability to adapt to changing market conditions and regulations. As the cost and availability of fuels fluctuates, industries need the flexibility to switch between different fuel sources to minimize operational costs and ensure uninterrupted production. Additionally, strict environmental regulations incentivize industries to invest in cleaner alternative fuels, such as natural gas and biofuels. Burner pipes that can accommodate these fuels help reduce emissions and improve environmental performance.
Additionally, fuel flexibility in the burner pipes is essential to maximize energy efficiency and process stability. Different fuels have unique combustion characteristics, such as ignition temperature, flame stability, and residence time. Burner pipes capable of optimizing the combustion of various fuels ensure consistent heat generation and better control of process variables. This not only improves energy efficiency but also improves the reliability and safety of industrial operations.
Additionally, fuel flexibility in burner pipes can contribute to the overall sustainability of industrial processes. By using a wider range of renewable and low-carbon fuels, industries can reduce their carbon footprint and their dependence on fossil fuels. This is part of global efforts to combat climate change and transition to a more sustainable energy future.
To achieve fuel flexibility, burner pipes must be designed and manufactured with the ability to accommodate different fuel types and operating conditions. This includes features such as variable geometry burners, fuel atomization systems and advanced combustion control technologies. Additionally, material selection and construction methods must be optimized to resist the corrosive and erosive effects of various fuel compositions.
Overall, the importance of fuel flexibility in burner lines is paramount to the modern industrial landscape. It allows industries to adapt to changing market conditions, comply with environmental regulations and improve energy efficiency. By investing in burner pipes that prioritize fuel flexibility, industries can future-proof their operations and contribute to a more sustainable and resilient energy sector.
The importance of fuel flexibility in burner pipes
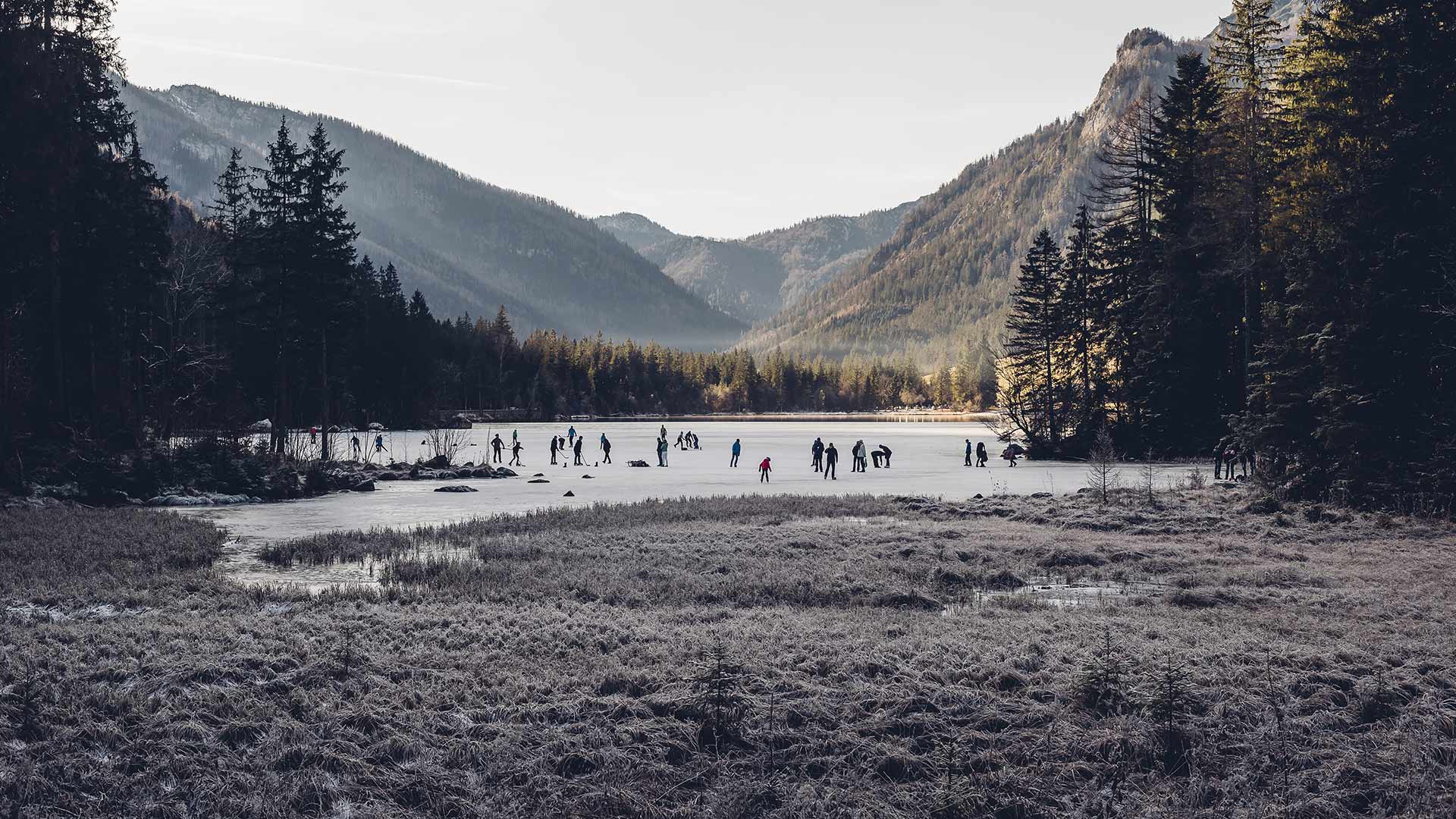