Incineration systems are used to safely dispose of waste through high temperature combustion. These systems are commonly used in industries such as healthcare, waste management and chemical processing. To ensure the safe and efficient operation of incineration systems, programmable logic controllers (PLCs) are often used to automate and control various processes. However, as technology and best practices continue to evolve, it is crucial for industries to reevaluate their PLC control systems in incineration systems.
One of the key considerations when re-evaluating PLC control in incineration systems is the need to incorporate advanced monitoring and diagnostic features. Thanks to advances in technology, controllers can now be equipped with sensors and monitoring devices that provide real-time data on incinerator temperature, pressure and emissions. By integrating these features into PLC control systems, operators can have better visibility into incinerator performance and quickly identify any issues that may arise. This not only helps avoid possible malfunctions, but also ensures compliance with environmental regulations.
In addition to advanced monitoring capabilities, the integration of predictive maintenance tools is also essential to re-evaluate PLC control in incineration systems. Predictive maintenance uses data analysis to predict when equipment maintenance should be performed based on the actual condition of the equipment. By integrating this functionality into PLC control systems, operators can plan maintenance activities proactively, minimizing downtime and the risk of unexpected failures.
Additionally, as sustainability and environmental impact become increasingly important in today’s industries, the re-evaluation of PLC control in incineration systems should also focus on optimizing efficiency energy and emissions monitoring. The controllers can be programmed to control the incinerator combustion process in a way that minimizes fuel consumption while meeting emissions standards. Additionally, integrating emissions monitoring sensors into PLC control systems allows operators to closely monitor and report on the environmental impact of the incinerator, ensuring compliance with regulatory requirements.
Another aspect to consider when reevaluating PLC control in incineration systems is cybersecurity. With the growing number of cyber threats targeting industrial control systems, it is crucial to ensure that controllers are properly secured against potential attacks. Industries should implement robust cybersecurity measures, such as network segmentation, access control, and regular software updates, to protect their Powerline control systems from unauthorized access and malicious activity.
Finally, it is important for industries to reevaluate their training and maintenance programs for personnel responsible for the operation and maintenance of PLC control systems in incineration systems. With the introduction of new features and technologies, operators and maintenance technicians must be properly trained to effectively operate and troubleshoot these systems. Additionally, regular maintenance and calibration of the controllers is essential to ensure their reliability and accuracy in controlling the incinerator processes.
In conclusion, as technology and best practices continue to evolve, it is essential for industries to re-evaluate their PLC control systems in incineration systems. By integrating advanced monitoring and diagnostic capabilities, predictive maintenance tools, energy efficiency and emissions monitoring, cybersecurity measures, and comprehensive training and maintenance programs, industries can ensure safe operation and efficiency of their incineration systems while minimizing their environmental impact. Reevaluation of PLC control in incineration systems is a crucial step to ensure the long-term success of these systems in various industries.
Re-evaluation of best practices for PLC control in incineration systems
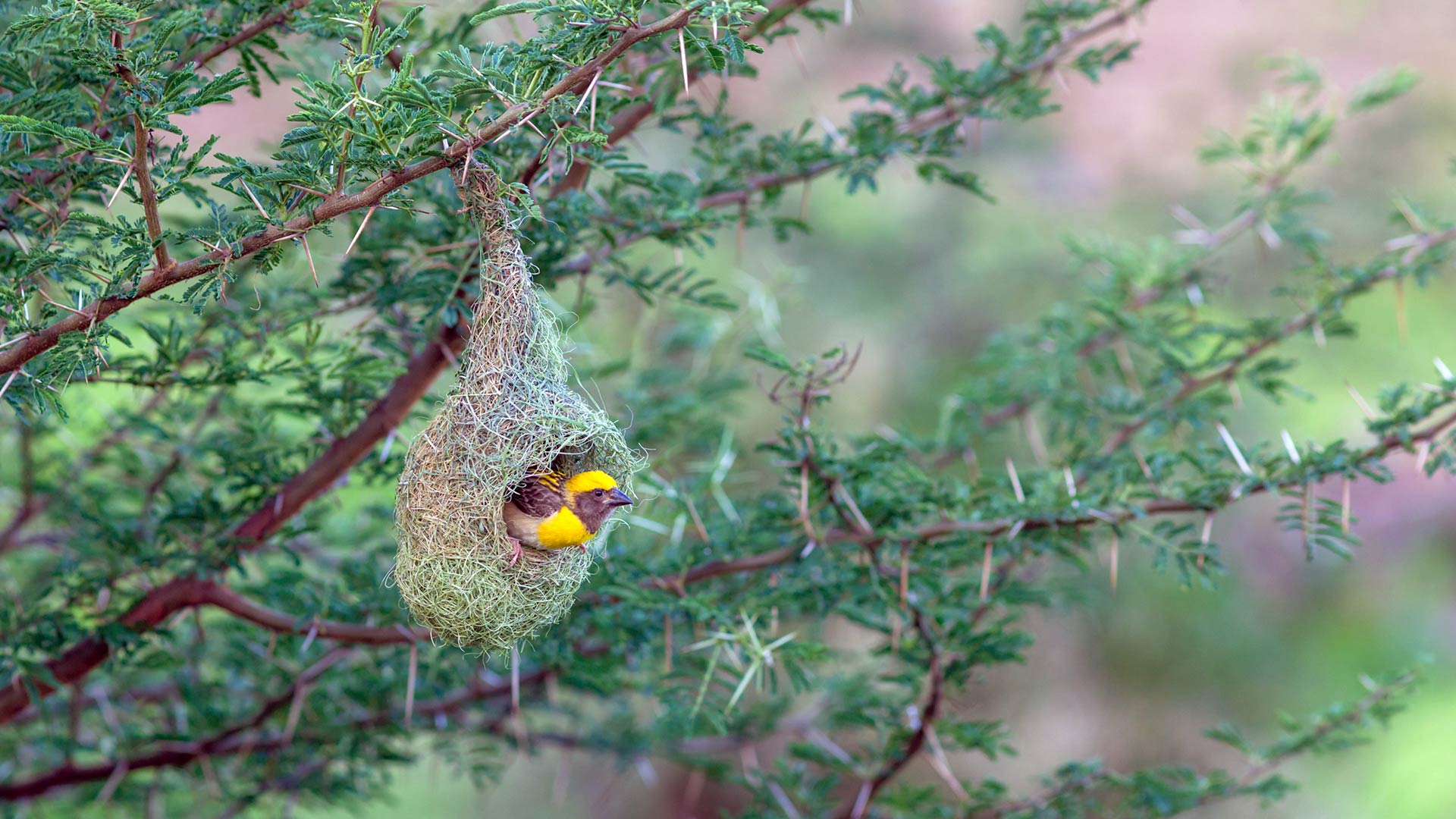