Refractory cement is a crucial component in various industries, such as steel, glass and cement production, where high temperatures and harsh conditions are the norm. This specialized cement is designed to resist extreme heat, corrosion and erosion, making it an essential material for lining kilns, kilns and other high-temperature equipment.
When it comes to selecting refractory cement, maximizing efficiency and durability are top priorities for companies. High-quality refractory cement is the key to achieving these goals, as it provides superior performance and longevity in demanding industrial environments.
One of the main benefits of using high quality refractory cement is its ability to withstand high temperatures without compromising its structural integrity. This is crucial for maintaining the efficiency of industrial processes, as it ensures that the lining of furnaces and furnaces remains intact even under the most extreme operating conditions.
In addition to withstanding high temperatures, high-quality refractory cement also has excellent resistance to chemical corrosion and erosion. This is essential to protect the integrity of the equipment and extend its life, reducing the need for frequent repairs and replacements.
Additionally, high-quality refractory cement is formulated to have low thermal conductivity, which helps minimize heat loss and improve the energy efficiency of industrial processes. By reducing heat loss, businesses can save on energy costs and improve their overall operational efficiency.
To maximize the effectiveness and durability of refractory cement, it is essential to carefully select a high-quality product that meets the specific application requirements. Factors to consider when choosing a high-quality refractory cement include its composition, bonding system and overall performance characteristics.
For example, high alumina refractory cement is known for its excellent resistance to high temperatures and abrasion, making it suitable for lining kilns and furnaces in industries such as steel production and of glass. On the other hand, calcium aluminate cement offers exceptional chemical resistance and is often used in applications where exposure to corrosive materials is a concern.
Additionally, the bonding system of the refractory cement plays a vital role in its performance and durability. High quality refractory cement is typically formulated with a strong bonding system that ensures excellent adhesion to the substrate, reducing the risk of delamination and premature failure.
To ensure optimal performance from high-quality refractory cement, it is essential to follow proper installation and maintenance practices. This involves ensuring the cement is applied according to the manufacturer’s directions and carrying out regular inspections to identify any signs of wear or damage.
In conclusion, maximizing efficiency and durability in industrial applications requires the use of high quality refractory cement. By selecting a high-performance product with superior resistance to high temperatures, corrosion and erosion, companies can improve the longevity of their equipment and improve operational efficiency. With the right refractory cement in place, companies can confidently meet the challenges of high-temperature environments and realize greater productivity and long-term cost savings.
Maximize efficiency and durability with high-quality refractory cement
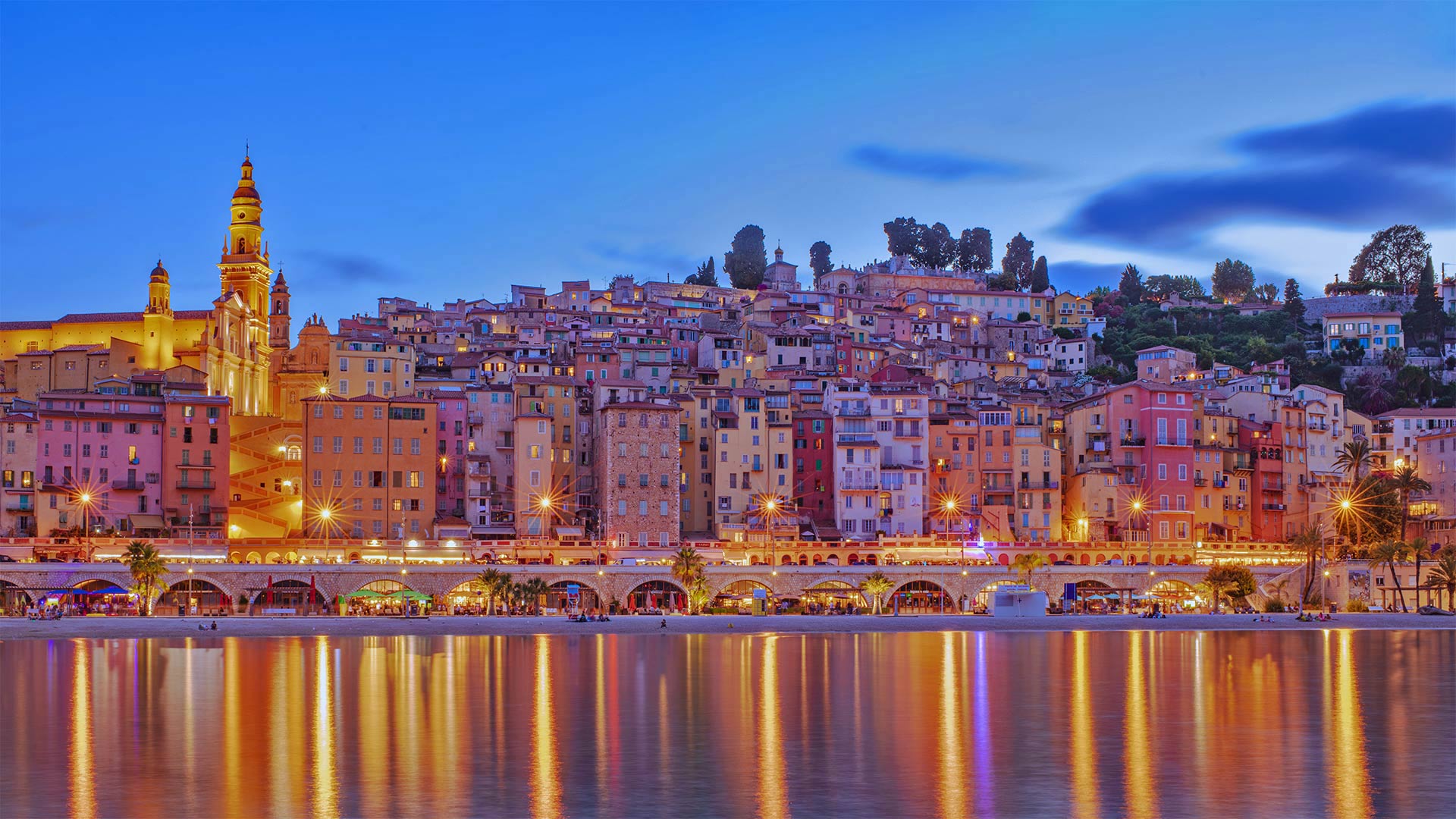