Combustion burners are essential components in a wide range of industrial and commercial processes, from heating and power generation to chemical processing and metal smelting. These devices are responsible for converting fuel into thermal energy through combustion and are available in different types to meet different applications and requirements. In this article, we will explore the applications and benefits of different types of combustion burners.
1. Conventional burners:
Conventional burners are widely used in commercial and residential heating systems, such as furnaces and boilers. They typically run on natural gas, propane or oil and are capable of producing a constant, controlled flame for space and water heating applications. The main advantage of conventional burners is their simplicity and reliability, which makes them suitable for a wide range of heating systems.
2. Low Nox emission burners:
Low NOx burners are designed to reduce emissions of nitrogen oxides (NOx) during the combustion process. As environmental regulations become more stringent, low NOx burners are becoming more prevalent in industrial and commercial applications, especially in areas with strict fuel quality requirements. air. These burners help reduce NOx by optimizing combustion efficiency and mixing air and fuel in a way that minimizes NOx formation.
3. Ultra-low NOx burners:
Ultra-low NOx burners are an advanced version of low NOx burners, enabling even greater reductions in nitrogen oxide emissions. These burners are commonly used in industrial boilers, power plants and chemical processing facilities, where control of NOx emissions is essential for compliance with environmental regulations. Ultra-low NOx burners typically incorporate advanced combustion technology, such as staged combustion and flue gas recirculation, to achieve ultra-low emissions without sacrificing combustion efficiency.
4. High speed burners:
High velocity burners are designed to produce a very turbulent and efficient combustion process, making them ideal for applications requiring high heat transfer rates and precise temperature control. These burners are commonly used in industrial furnaces, incinerators and metal smelting applications, where rapid and efficient combustion of fuel is essential to maintain process performance and optimize energy efficiency.
5. Radiant tube burners:
Radiant tube burners are used in applications that require uniform, high-intensity heat transfer, such as in industrial furnaces, heat treating ovens, and drying processes. These burners typically consist of a tube that radiates heat directly to the material being processed, resulting in rapid and even heating. The benefits of radiant tube burners include precise temperature control, high thermal efficiency and reduced heat loss through radiation.
In conclusion, combustion burners play a crucial role in a wide range of industrial and commercial processes, and the choice of burner type can have a significant impact on process performance and efficiency. By understanding the applications and benefits of different burner types, engineers and facility managers can select the burner best suited to their specific needs, from reducing emissions to improving efficiency. energy or optimize heat transfer. As combustion technology continues to advance, the development of new burner types and technologies is expected to further improve the efficiency and environmental impact of combustion processes.
Applications and advantages of various types of combustion burners
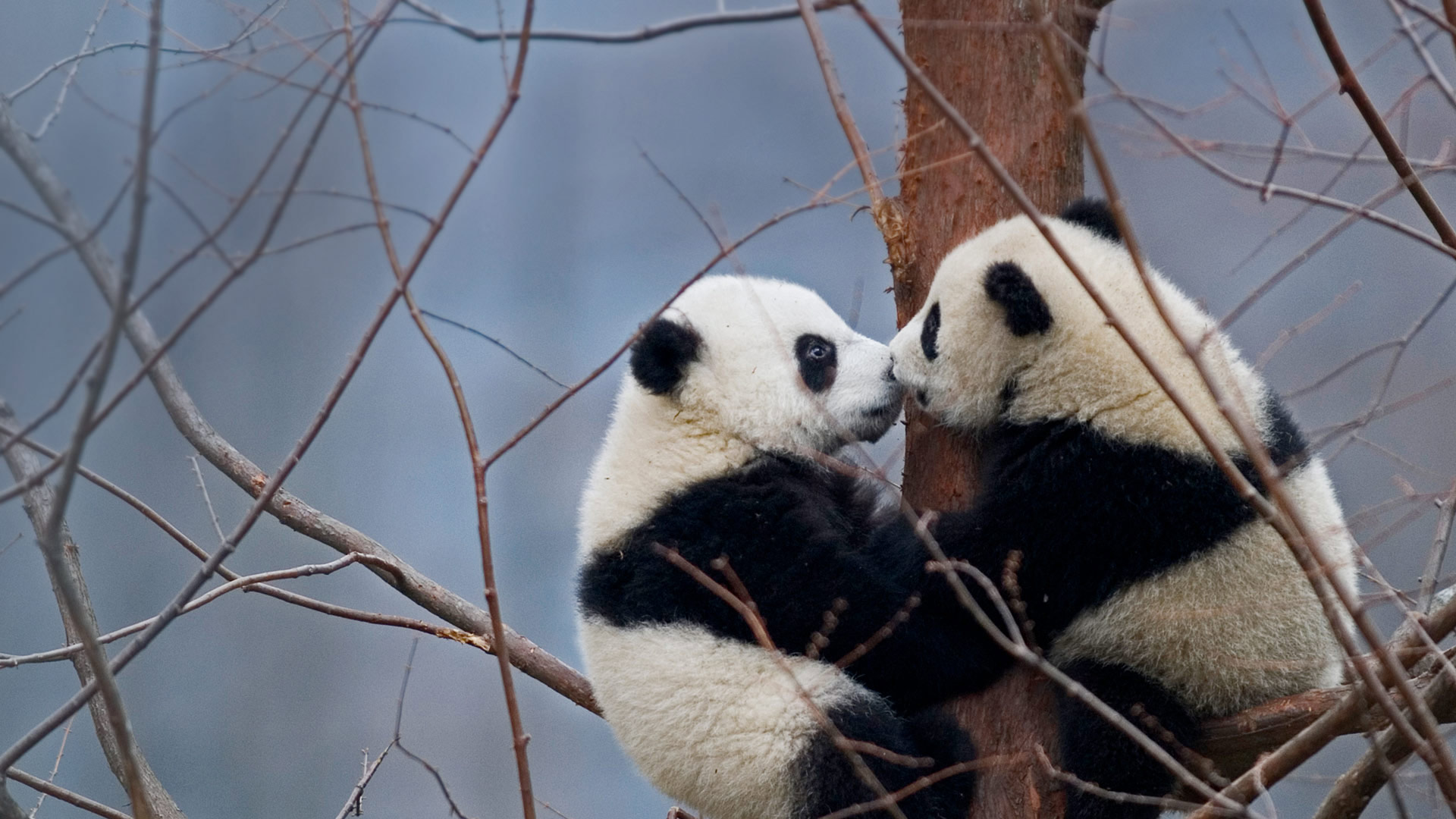