Evaluating the Cost-Effectiveness of Smoke Filter Chambers (Dry Scrubbers) for Businesses
With increasing regulations on air emissions and a growing awareness of the impact of industrial processes on the environment, businesses are under pressure to adopt more sustainable practices. One area of focus is the reduction of smoke and particulate emissions from industrial processes. Smoke filter chambers, also known as dry scrubbers, are one technology that businesses are turning to in order to achieve this goal.
Smoke filter chambers are designed to remove particulate matter and other pollutants from industrial exhaust gases. This can lead to cleaner air emissions and a reduced impact on the environment. However, businesses must carefully evaluate the cost-effectiveness of installing and operating smoke filter chambers to determine if they are a viable solution for their specific needs.
The Cost of Installation
The initial cost of installing a smoke filter chamber can vary significantly depending on the size and complexity of the system. Larger industrial facilities may require multiple chambers and additional equipment to effectively capture and remove pollutants from their exhaust gases. Additionally, businesses must consider the cost of any modifications that may be needed to their existing infrastructure to accommodate the new equipment.
One of the most significant factors influencing the cost of installation is the type of pollutants being emitted. Some pollutants are more difficult to capture and remove, requiring more sophisticated technology and higher installation costs. Therefore, a thorough assessment of the specific emissions from an industrial process is essential before determining the cost of installing a smoke filter chamber.
Operating and Maintenance Costs
Once installed, smoke filter chambers require regular maintenance and operation to ensure they continue to function effectively. Businesses must consider the ongoing costs of maintaining the equipment, including the replacement of filters and other components, as well as the energy usage required to operate the system.
There is also the potential for additional costs associated with compliance testing and reporting. Many jurisdictions require businesses to regularly monitor and report their emissions, and the installation of smoke filter chambers may require additional testing and reporting procedures.
Cost Savings and Benefits
Despite the initial and ongoing costs, there are potential cost savings and benefits to be gained from the installation of smoke filter chambers. Not only can businesses reduce their environmental impact and meet regulatory requirements, but they may also decrease their operating costs in the long term.
By capturing and removing pollutants from their exhaust gases, businesses can limit the wear and tear on their equipment and reduce the need for costly repairs and maintenance. Additionally, some jurisdictions offer financial incentives for businesses that invest in emissions-reducing technologies, such as tax credits and grants.
FAQs
Q: What types of pollutants can smoke filter chambers remove?
A: Smoke filter chambers are designed to remove a wide range of pollutants, including particulate matter, sulfur dioxide, nitrogen oxides, and volatile organic compounds.
Q: How often do smoke filter chambers need to be maintained?
A: The frequency of maintenance depends on the specific system and the level of pollutants being emitted. Generally, filters need to be replaced on a regular basis, and the equipment should be inspected periodically to ensure it is functioning properly.
Q: Are there government incentives for businesses to install smoke filter chambers?
A: Many governments offer financial incentives for businesses to invest in emissions-reducing technologies, such as tax credits and grants. Businesses should check with their local environmental agencies to see what incentives are available in their area.
Evaluating the Cost-Effectiveness of Smoke Filter Chambers (Dry Scrubbers) for Businesses
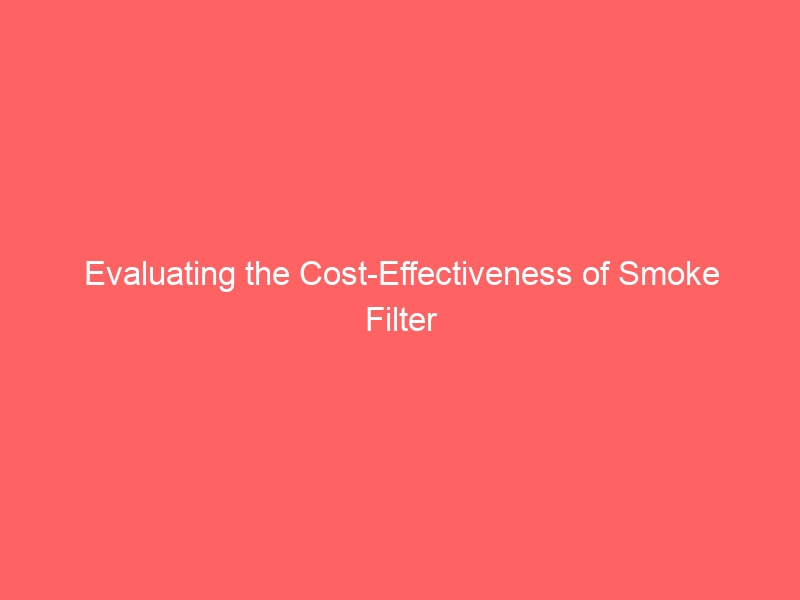