High aluminum refractory cement is a specialized type of cement engineered to withstand high temperatures and harsh conditions. It is commonly used in industries such as steelmaking, foundries, and glassmaking, where extreme heat and chemical exposure are common. The science behind high aluminum refractory cement is fascinating and complex, involving a careful balance of ingredients and precise chemical reactions.
One of the key components of high aluminum refractory cement is aluminum oxide (Al2O3). This compound is essential for its high melting point and excellent thermal conductivity, making it ideal for use in high-temperature environments. The amount of aluminum oxide in the cement is typically around 50%, giving it the high aluminum content that is essential for its performance.
Another important component of high aluminum refractory cement is calcium oxide (CaO). This compound acts as a flux, helping to lower the melting point of the cement and improve its flow properties at high temperatures. The calcium oxide content in high aluminum refractory cement is typically around 50%, contributing to its excellent workability and resistance to thermal shock.
In addition to aluminum and calcium oxides, high aluminum refractory cement also contains other additives and materials to improve its properties. These may include silica, magnesia, and other refractory materials that enhance its strength, durability, and resistance to chemical corrosion.
The production process for high aluminum refractory cement involves carefully controlled blending of the raw materials, followed by high-temperature firing in a kiln. During the firing process, the raw materials undergo a series of chemical reactions that result in the formation of new compounds, including calcium aluminate phases that contribute to the cement’s high-temperature performance.
The precise chemical composition and microstructure of high aluminum refractory cement are critical to its performance in high-temperature applications. The aluminum oxide and calcium oxide content, as well as the presence of other refractory materials, determine the cement’s ability to withstand thermal cycling, chemical attack, and mechanical stress. The careful balance of these ingredients is a result of extensive research and development in the field of refractory materials science.
High aluminum refractory cement is typically supplied in a powdered form and mixed with water to form a paste that can be applied to the surfaces of refractory linings or used to bond refractory bricks and shapes together. Once the cement has set and cured, it forms a strong, heat-resistant bond that protects the underlying refractory materials from the harsh conditions of high-temperature processes.
In conclusion, high aluminum refractory cement is a remarkable product that relies on the principles of materials science and chemistry to deliver exceptional performance in high-temperature applications. Its unique combination of aluminum oxide, calcium oxide, and other additives, along with controlled manufacturing processes, ensures that it can withstand the extreme conditions of industrial processes. The science behind high aluminum refractory cement is a testament to the ingenuity and innovation of materials engineers and chemists, and it continues to play a crucial role in enabling the production of steel, glass, and other essential materials.
The Science Behind High Aluminum Refractory Cement: AL2O350 CA50 A600(Kg)
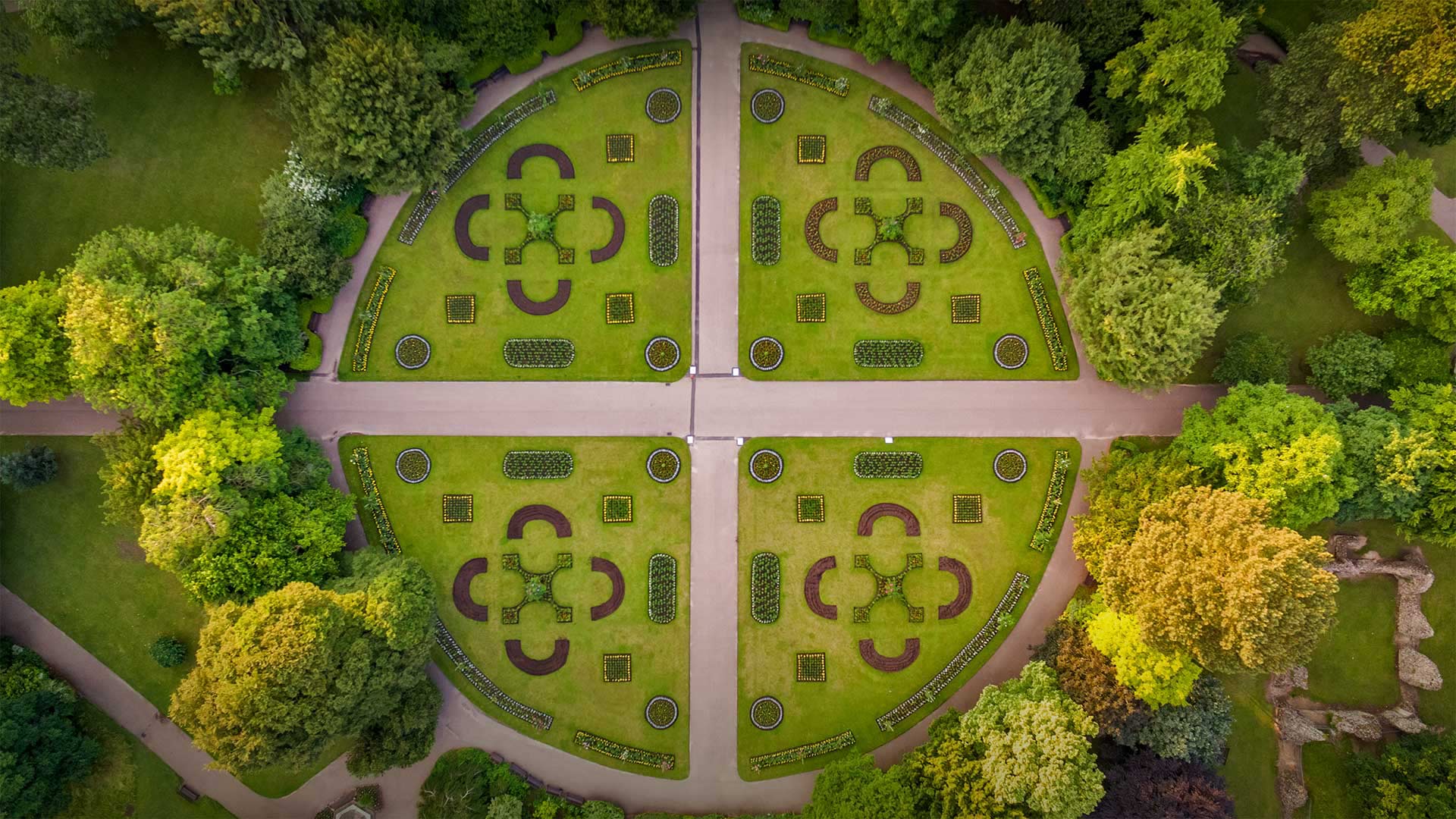