In various industries such as pharmaceuticals, food processing, and manufacturing, maintaining precise temperature control in primary chambers is essential for ensuring product quality and process efficiency. Traditional manual temperature control methods are often inefficient and prone to human error, leading to inconsistent temperatures and wasted energy. However, with the advancements in digital temperature control technology, businesses can maximize their efficiency and productivity while minimizing costs.
Digital temperature control systems offer numerous benefits that can significantly improve the performance of primary chamber parameters. These systems utilize advanced sensors and programmable logic controllers (PLCs) to monitor and adjust temperatures with precision. The digital interface allows operators to set specific temperature parameters and receive real-time data on chamber conditions, providing a level of control and accuracy that was previously unattainable with manual methods.
One of the key advantages of digital temperature control is its ability to maintain consistent and stable temperatures within primary chambers. This is crucial for processes that require precise temperature control, such as chemical reactions, crystallization, and sterilization. By eliminating fluctuations and maintaining the desired temperature levels, digital control systems ensure product quality and reduce the risk of batch failures or inconsistencies.
Additionally, digital temperature control systems offer energy-saving capabilities that can lead to substantial cost reductions. These systems can be programmed to optimize heating and cooling cycles, reducing energy consumption and minimizing waste. By precisely regulating temperature levels and minimizing unnecessary heating or cooling, businesses can see significant savings on their energy bills while also reducing their environmental impact.
Furthermore, digital temperature control allows for remote monitoring and control, enabling operators to manage chamber parameters from anywhere with internet access. This feature is particularly valuable for businesses with multiple production facilities or for those that require 24/7 monitoring. Operators can receive alerts for temperature fluctuations and make immediate adjustments to ensure that processes remain on track, minimizing downtime and preventing potential product spoilage.
In addition to improving process efficiency, digital temperature control systems also offer data logging and analysis capabilities. This allows businesses to track temperature trends over time, identify patterns, and make data-driven decisions to optimize their processes. By analyzing temperature data, businesses can identify opportunities for improvement, troubleshoot issues, and make proactive adjustments to enhance overall performance.
Overall, digital temperature control systems offer a comprehensive solution for maximizing efficiency in primary chamber parameters. By providing precise temperature control, energy savings, remote monitoring, and data analysis capabilities, these systems can significantly improve product quality, reduce costs, and enhance overall productivity. Businesses that invest in digital temperature control technology can expect to see a rapid return on investment and gain a competitive edge in their respective industries.
Maximizing Efficiency with Digital Temperature Control in Primary Chamber Parameters
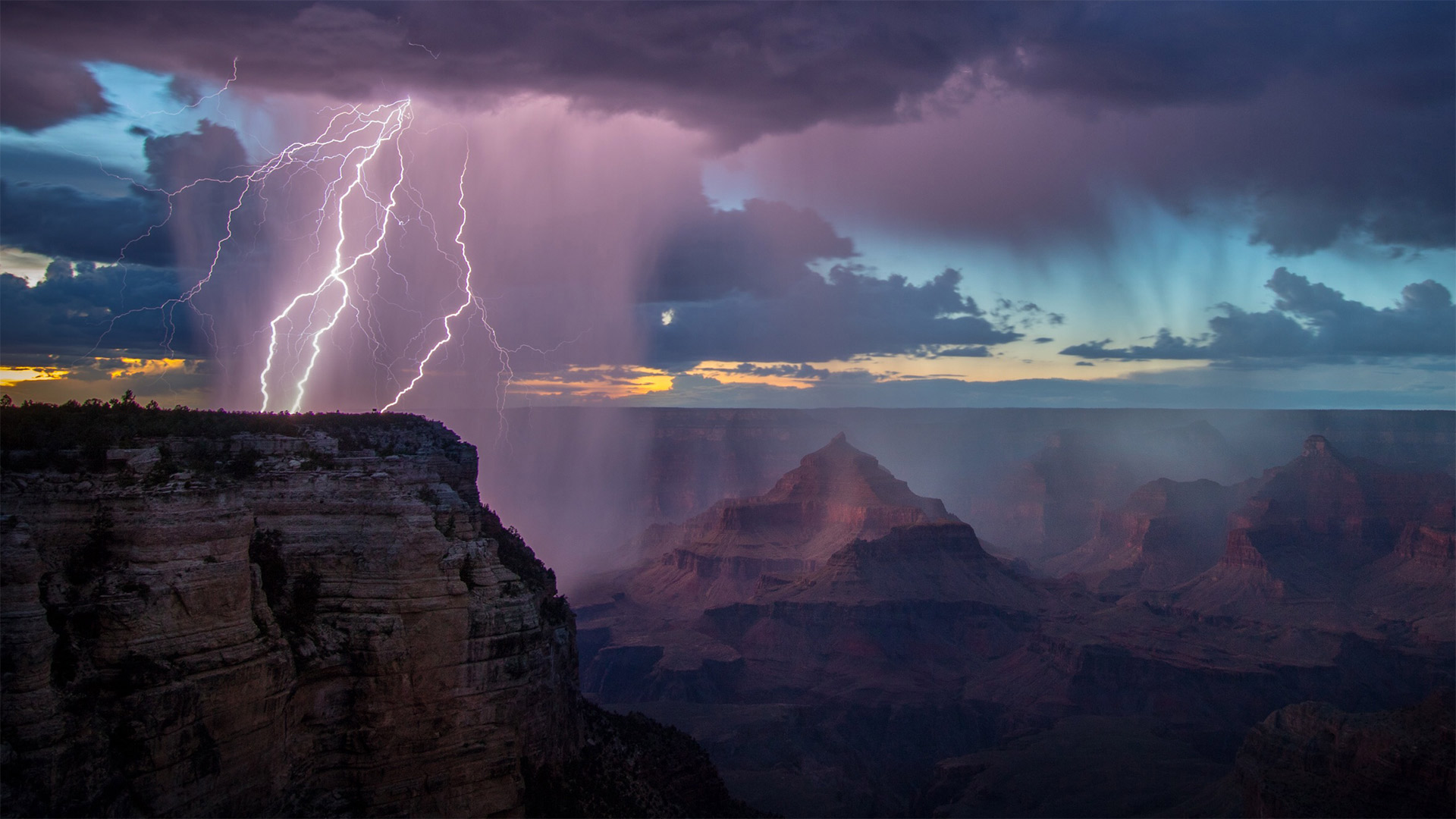