Refractory cement is a vital component in many industrial and commercial settings, used to build and repair high-temperature applications such as ovens, kilns, and furnaces. Proper installation and maintenance of refractory cement are crucial to ensure the longevity and efficiency of these high-heat environments. Here are some key tips for properly installing and maintaining refractory cement.
1. Follow manufacturer’s instructions: Different types of refractory cement have varying installation and maintenance requirements. It’s important to carefully read and follow the manufacturer’s instructions and guidelines for the specific product you are using.
2. Surface preparation: Before installing refractory cement, it’s crucial to prepare the surface properly. The surface should be clean, dry, and free of any loose debris, oil, or grease. Any existing refractory material should be removed or repaired as needed.
3. Mixing: Refractory cement should be mixed according to the manufacturer’s instructions. It’s important to mix the cement thoroughly to ensure a consistent and homogenous mixture. Overmixing or undermixing can result in a weak and less effective refractory lining.
4. Application: When applying refractory cement, it’s important to use the proper tools and techniques. The cement should be spread evenly and firmly packed to ensure a strong and durable bond. It’s also important to take into account the specific application and temperature requirements, as different types of refractory cement have different heat resistance properties.
5. Curing: After the refractory cement has been applied, it needs to cure properly to achieve its maximum strength and heat resistance. The curing process usually involves allowing the cement to air dry for a specified amount of time, followed by a controlled heat-up process to gradually reach the operating temperature.
6. Maintenance: Regular maintenance is essential for preserving the effectiveness of refractory cement. Inspect the refractory lining regularly for any signs of wear, damage, or erosion. Any cracks or gaps should be repaired promptly to prevent heat leakage and potential structural damage.
7. Cleaning: Keeping the refractory lining clean is also important for maintaining its performance. Remove any accumulated ash, soot, or debris that can impede the efficiency of the cement.
8. Professional assistance: For complex or large-scale installations, it’s advisable to seek the help of a professional refractory contractor. They have the expertise and experience to ensure the proper installation and maintenance of refractory cement, which is critical for the safety and efficiency of high-temperature applications.
In conclusion, proper installation and maintenance of refractory cement are essential for ensuring the longevity and efficiency of high-heat environments. By following the manufacturer’s guidelines, taking proper preparation and application steps, and conducting regular inspections and maintenance, you can maximize the performance and lifespan of your refractory cement.
How to Properly Install and Maintain Refractory Cement
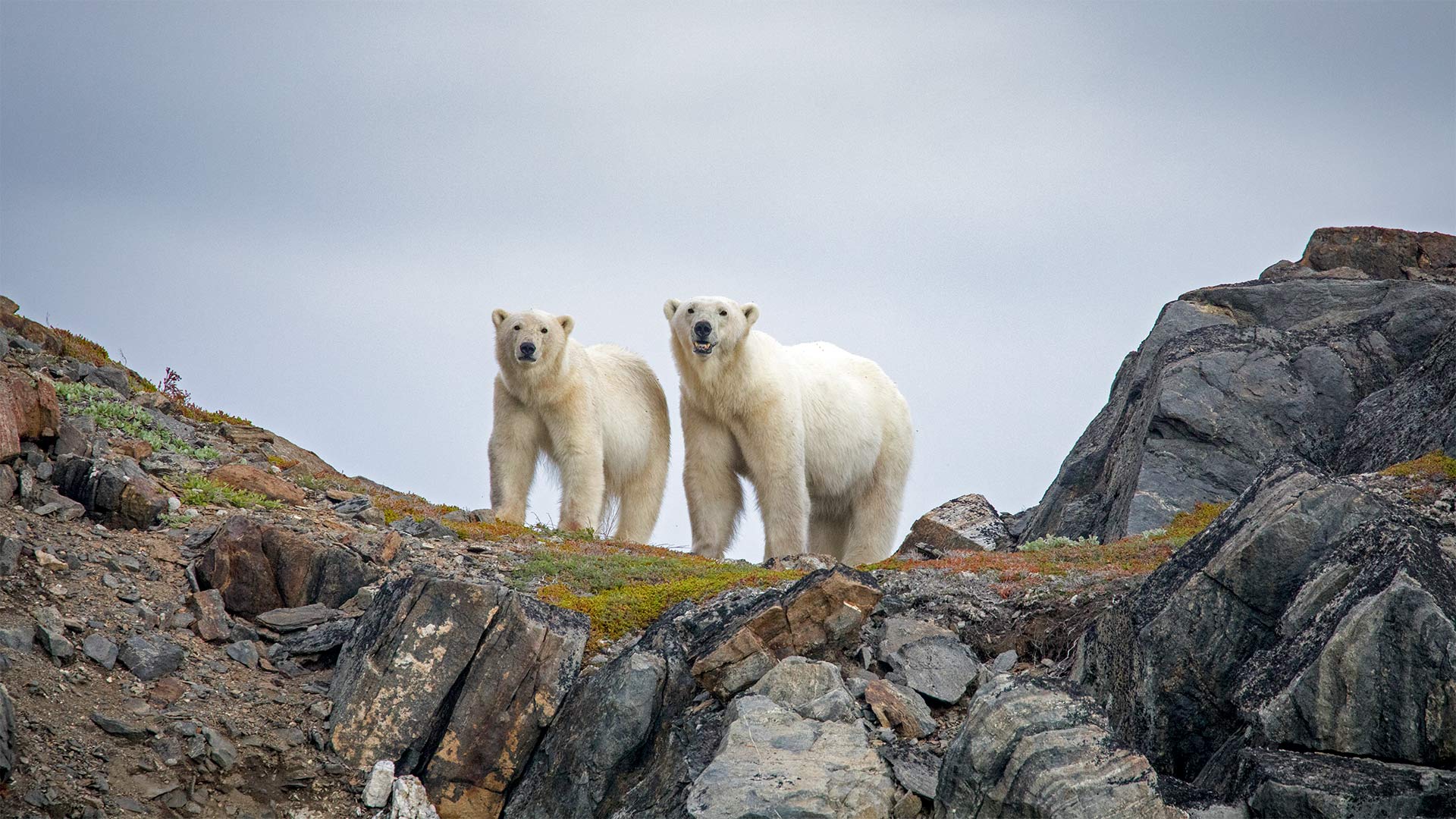