Refractory cement is a versatile and high-temperature resistant cement that is used in a variety of industrial applications. It is specially formulated to withstand extreme temperatures and harsh conditions, making it a crucial component in industries such as steel production, cement manufacturing, and petrochemical processing. Refractory cement is made from a variety of materials, including alumina, silica, and calcium, which give it the ability to withstand temperatures in excess of 3000°F (1650°C).
There are several different types of refractory cement, each with its own unique properties and applications. Here, we explore some of the most common types of refractory cement and their uses.
1. Conventional Refractory Cement:
Conventional refractory cement, also known as high-temperature cement, is a general-purpose refractory material that is commonly used in industrial applications. It is highly resistant to heat and can withstand temperatures up to 3000°F (1650°C). Conventional refractory cement is often used for lining furnaces, kilns, and other high-temperature processing equipment.
2. Low Cement Refractory Cement:
Low cement refractory cement is a type of refractory material with a low cement content, typically less than 2%. This results in a highly dense and strong material with excellent resistance to abrasion, thermal shock, and chemical attack. Low cement refractory cement is commonly used in applications where high strength and durability are required, such as in steelmaking and foundry operations.
3. Insulating Refractory Cement:
Insulating refractory cement is designed to provide thermal insulation in high-temperature applications. It has a low thermal conductivity, making it ideal for use in environments where heat loss needs to be minimized. Insulating refractory cement is commonly used for lining kilns, boilers, and ovens, as well as in the construction of fireplaces and chimneys.
4. Refractory Mortar:
Refractory mortar is a special type of refractory cement that is used to bond refractory bricks and other refractory materials together. It is formulated to withstand the high temperatures and harsh conditions found in industrial furnaces and kilns. Refractory mortar is available in a variety of formulations, including air setting, heat setting, and hydraulic setting, to suit different applications.
5. Alumina Refractory Cement:
Alumina refractory cement is made primarily from alumina, which gives it exceptional resistance to high temperatures and chemical corrosion. It is commonly used in applications where high purity and thermal stability are required, such as in the production of ceramics, glass, and electronic components.
In conclusion, refractory cement is an essential material in a wide range of industrial applications, where extreme temperatures and harsh conditions are common. With its ability to withstand heat, abrasion, and chemical attack, refractory cement plays a crucial role in maintaining the integrity and functionality of high-temperature processing equipment. By understanding the different types of refractory cement available, industries can choose the right material for their specific needs and ensure the longevity and efficiency of their operations.
Exploring the Different Types of Refractory Cement
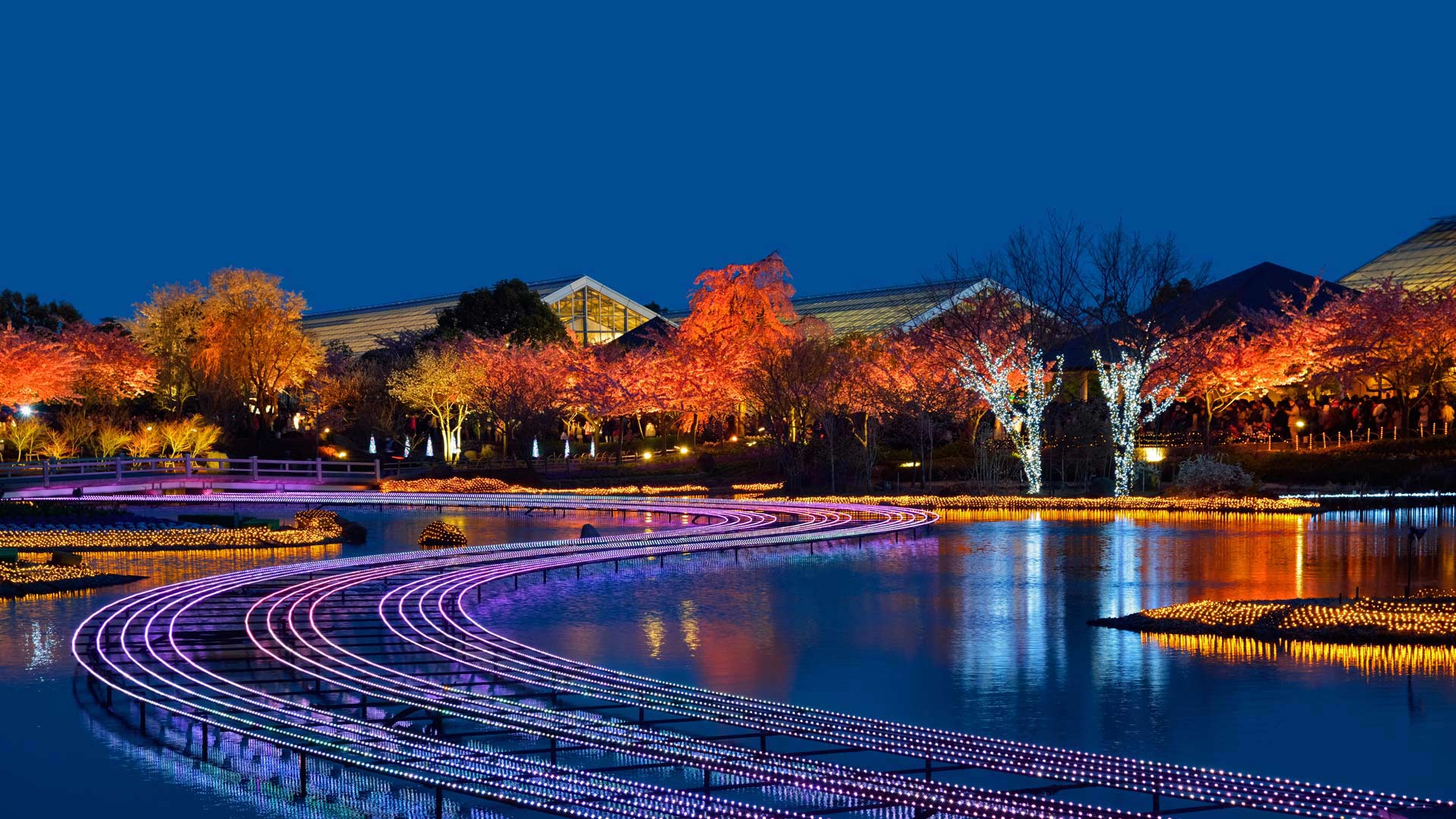