Revolutionary Flange Gasket Technology Ensures Burner Safety in Waste Incinerators
Waste incinerators are essential for the safe and effective disposal of various types of waste, including medical, industrial, and municipal waste. However, the operation of these incinerators comes with inherent safety risks, particularly when it comes to the burner system. Ensuring the safety and efficiency of the burner system is critical to prevent accidents and effectively control the incineration process.
One key component that plays a crucial role in burner safety is the flange gasket. Flange gaskets are used to create a seal between two flanged components, such as pipes or valves, to prevent leakage and maintain a tight seal under high-temperature and high-pressure conditions. In waste incinerators, the flange gaskets must withstand extreme temperatures, corrosive chemicals, and high-pressure fluctuations, making them a critical component for ensuring the safety and efficiency of the burner system.
Traditional flange gasket materials, such as rubber, paper, or asbestos, have limitations in terms of their ability to withstand the harsh conditions present in waste incinerators. These materials can degrade over time, leading to leaks, and ultimately, compromising the safety and efficiency of the burner system. Additionally, these materials may pose health and environmental hazards due to their composition.
To address these challenges, revolutionary flange gasket technology has been developed to ensure burner safety in waste incinerators. These new gasket materials are designed to withstand extreme temperatures, corrosive chemicals, and high-pressure conditions, providing a reliable and long-lasting seal for flanged components in waste incinerators.
One such revolutionary flange gasket material is graphite gasket technology. Graphite gaskets are made from high-purity graphite and are designed to withstand extreme temperatures, corrosive chemicals, and high-pressure conditions. They provide an excellent seal, even under the most demanding operating conditions, making them an ideal choice for burner safety in waste incinerators.
Graphite gaskets offer several key advantages over traditional gasket materials. They have high thermal stability, which allows them to maintain their sealing properties even at temperatures exceeding 1000°C. They are also resistant to a wide range of chemicals, making them suitable for use in waste incinerators where corrosive chemicals are present. Additionally, graphite gaskets have excellent compressibility and recovery properties, ensuring a tight and reliable seal under high-pressure conditions.
By using revolutionary flange gasket technology, waste incinerator operators can ensure the safety and efficiency of their burner systems. The use of high-performance gasket materials, such as graphite gaskets, can prevent leaks and ensure that the incineration process is effectively controlled. This not only minimizes the risk of accidents but also contributes to environmental protection by preventing the release of harmful substances into the atmosphere.
In conclusion, revolutionary flange gasket technology, such as graphite gaskets, plays a vital role in ensuring the safety of burner systems in waste incinerators. These high-performance gasket materials are designed to withstand extreme temperatures, corrosive chemicals, and high-pressure conditions, providing a reliable and long-lasting seal for flanged components. By utilizing these innovative gasket materials, waste incinerator operators can effectively control the incineration process and prevent accidents, ultimately contributing to a safer and more sustainable waste management solution.
Revolutionary Flange Gasket Technology Ensures Burner Safety in Waste Incinerators
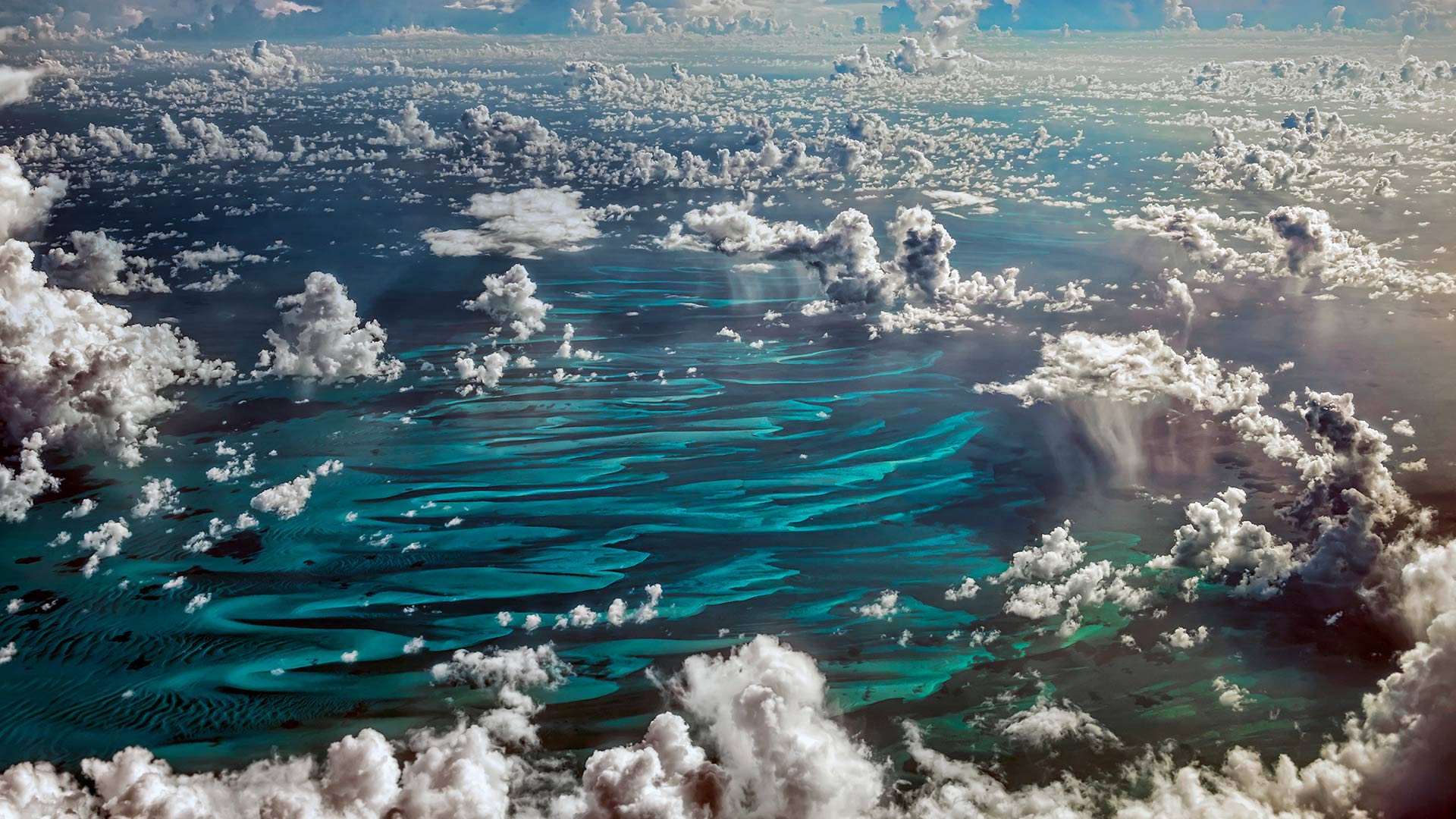