Refractory cement is a special type of cement used in high temperature applications, such as in kilns, kilns and incinerators. It is designed to withstand the extreme temperatures and harsh conditions of industrial processes, making it an essential material in many manufacturing and production industries. However, the production and use of refractory cement can have significant environmental impacts and it is important to consider its sustainability.
The environmental impact of refractory cement begins from its production. The manufacturing process requires high energy input and produces a large amount of greenhouse gas emissions. Raw materials used in the production of refractory cement, such as alumina, silica and other minerals, are typically extracted from the earth, resulting in the destruction of habitats and disruption of ecosystems. Additionally, the high-temperature baking process used to create refractory cement releases pollutants, including particulate matter and carbon dioxide, into the atmosphere.
In addition to the environmental impact of its production, the use of refractory cement can also contribute to environmental issues. When refractory cement is used in industrial processes, it is often subjected to extreme temperatures and harsh chemical environments, leading to wear and degradation over time. This may require frequent repairs and replacements, leading to increased waste and resource consumption.
Despite these environmental challenges, efforts are being made to improve the durability of refractory cement. One approach is to develop alternative materials and manufacturing processes that reduce the environmental impact of production. For example, researchers are exploring the use of alternative raw materials, such as industrial waste or recycled materials, to create refractory cement. Additionally, efforts are being made to optimize the cooking process to reduce energy consumption and emissions.
Another approach to improving the durability of refractory cement is to focus on extending its lifespan and reducing the need for frequent replacements. This can be achieved through the development of advanced refractory materials that provide improved durability and resistance to wear and degradation. Additionally, implementing proper maintenance and repair practices can help extend the life of refractory cement and minimize waste generation.
In conclusion, although refractory cement is essential to many industrial processes, its production and use can have significant environmental impacts. Efforts to improve the sustainability of refractory cement are important to reduce its environmental footprint and ensure that it can continue to meet the needs of the industry in a more sustainable manner. By investing in research and development and implementing sustainable practices, the environmental impact of refractory cement can be minimized, contributing to a more sustainable future for the industry.
The environmental impact and sustainability of refractory cement
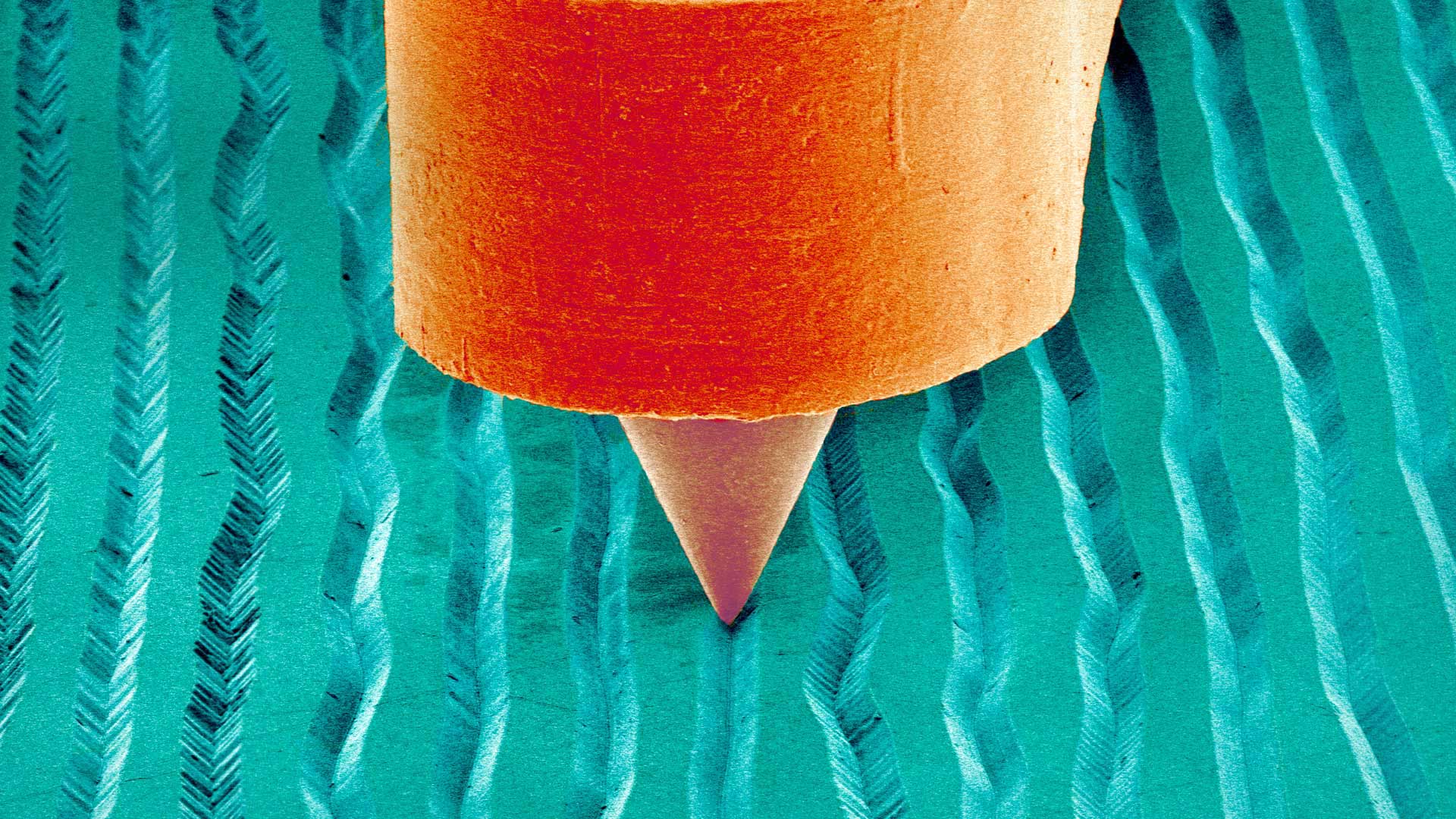