Refractory cement, also known as calcium aluminate cement, is a crucial material in industries such as steel, cement and glass manufacturing. It is used to cover ovens, ovens and other high temperature appliances to resist intense heat and protect surrounding equipment. As technology continues to advance, innovations in refractory cement have been introduced to improve performance, durability and efficiency. Here’s what you need to know about the latest developments in refractory cement technology.
One of the key innovations in refractory cement technology is the development of low-cement and ultra-low-cement concretes. These materials have lower porosity and higher strength than traditional refractory cement, making them more resistant to thermal shock and chemical erosion. They also provide improved fluidity during installation, allowing for easier and faster coating of equipment. Additionally, low-cement and ultra-low-cement concretes have better adhesion to the substrate, resulting in reduced material consumption and extended service life.
Another advancement in refractory cement technology is the use of nanotechnology to improve the properties of refractory materials. Nanoparticles, such as carbon nanotubes and alumina nanoparticles, are added to refractory cement to improve mechanical strength, thermal conductivity and corrosion resistance. The result is a more durable and better performing material capable of withstanding harsh operating conditions in an industrial environment.
Additionally, the development of alumina-magnesia-carbon (AMC) refractories has revolutionized the industry by providing superior resistance to thermal shock and erosion. These materials are highly sought after for their ability to withstand extreme temperatures and harsh chemical environments, making them ideal for use in high-wear areas of refractory linings.
In addition to material improvements, advances in application techniques have also contributed to the evolution of refractory cement technology. New installation methods, such as gunning, shotcreting and pumping, enable faster and more efficient coating of equipment, reducing downtime and maintenance costs. These techniques also ensure a more uniform and denser coating, leading to improved performance and longevity.
Additionally, the introduction of digital technologies, such as sensors and monitoring systems, has enabled real-time monitoring of refractory performance and condition. This enables proactive maintenance and predictive repair planning, avoiding costly downtime and equipment failure.
Overall, innovations in refractory cement technology have led to significant improvements in performance, durability and efficiency. These advances have enabled the development of materials and techniques that can better withstand the demanding conditions of industrial processes, thereby improving productivity and reducing operational costs. As technology continues to evolve, the future of refractory cement looks bright, with potential for even greater advancements in material properties and application methods.
Innovations in refractory cement technology: what you need to know
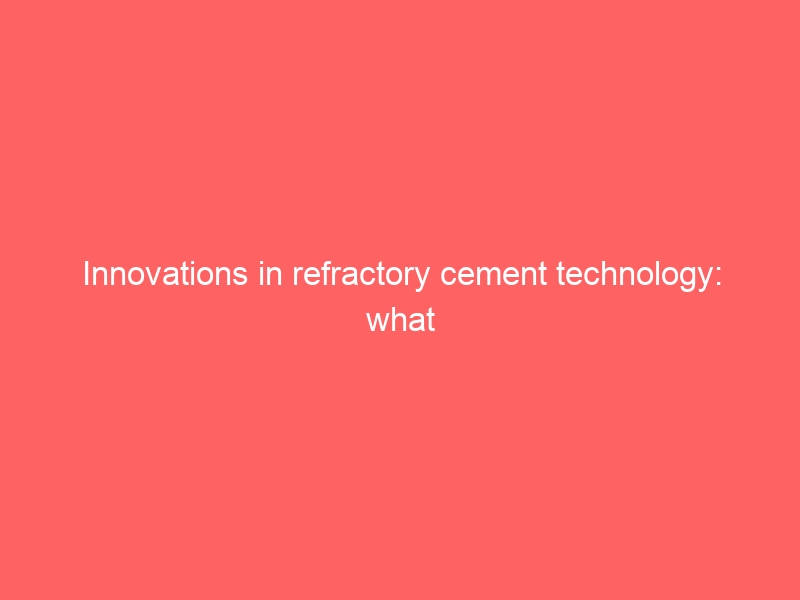