The combustion chamber is a critical component of an internal combustion engine, responsible for housing the fuel and air mixture and igniting it to produce power. The evolution of combustion chambers has been a fascinating journey, from early designs to modern engineering. Let’s explore this evolution and how it has shaped the performance of engines today.
Early combustion chambers were simple in design, often consisting of a bowl-shaped cavity in the cylinder head. This design was effective at mixing the fuel and air, but it had limitations when it came to controlling combustion and emissions. As engine technology advanced, so too did the combustion chamber.
One of the key advancements in combustion chamber design was the introduction of the hemispherical chamber, popularized by Chrysler in the 1950s. The hemispherical shape allowed for better airflow and improved combustion efficiency, leading to increased power and fuel economy. This design was a major leap forward in engine performance and was adopted by other manufacturers as well.
In the 1970s, the introduction of computer-aided design (CAD) and computational fluid dynamics (CFD) revolutionized combustion chamber engineering. Engineers could now accurately model and optimize the shape and dimensions of the combustion chamber for maximum efficiency and performance. This led to the development of complex shapes and features, such as squish pads, tumble ports, and swirl chambers, which helped improve combustion stability and reduce emissions.
Another significant milestone in combustion chamber evolution was the use of direct fuel injection. Traditional engines use port fuel injection, where the fuel is injected into the intake port before it enters the combustion chamber. Direct fuel injection, on the other hand, injects fuel directly into the combustion chamber, allowing for more precise control over the fuel-air mixture and combustion process. This technology has become increasingly popular in modern engines and has contributed to improved fuel efficiency and power output.
Today, combustion chambers are designed with a combination of advanced materials, precision engineering, and cutting-edge technologies. The goal is to achieve optimal combustion efficiency, power output, and emissions performance. Engine manufacturers are constantly pushing the boundaries of combustion chamber design to meet increasingly stringent emissions regulations and consumer demands for performance and efficiency.
One of the latest trends in combustion chamber design is the use of variable valve timing and lift systems. These systems allow for greater control over the intake and exhaust valves, enabling the engine to dynamically adjust the combustion process based on operating conditions. This results in improved efficiency, power output, and emissions performance across a wider range of engine speeds and loads.
In conclusion, the evolution of combustion chambers has been driven by the relentless pursuit of better efficiency, performance, and emissions control. From early designs to modern engineering, combustion chambers have undergone significant advancements that have revolutionized the way internal combustion engines operate. As technology continues to advance, we can expect combustion chamber design to play an increasingly critical role in shaping the future of automotive propulsion.
FAQs
Q: What is a combustion chamber?
A: A combustion chamber is a component of an internal combustion engine where the fuel and air mixture is ignited to produce power.
Q: Why is combustion chamber design important?
A: The design of the combustion chamber directly influences the performance, efficiency, and emissions of an engine.
Q: What are some modern advancements in combustion chamber design?
A: Modern advancements include the use of computer-aided design, direct fuel injection, variable valve timing, and lift systems.
Q: How has combustion chamber design evolved over time?
A: Combustion chamber design has evolved from simple bowl-shaped cavities to complex shapes and features optimized for maximum efficiency and performance.
The Evolution of Combustion Chambers: From Early Designs to Modern Engineering
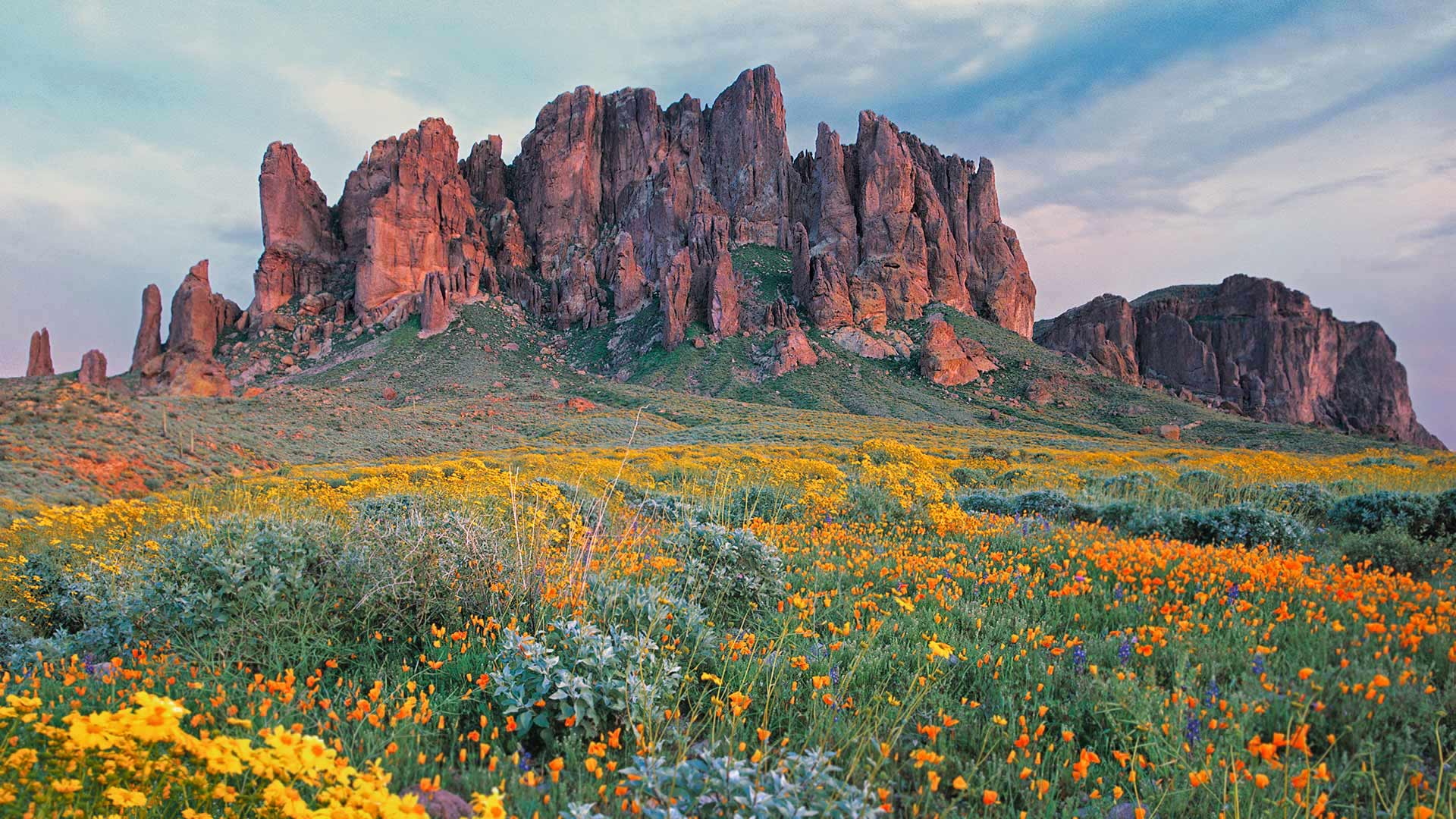